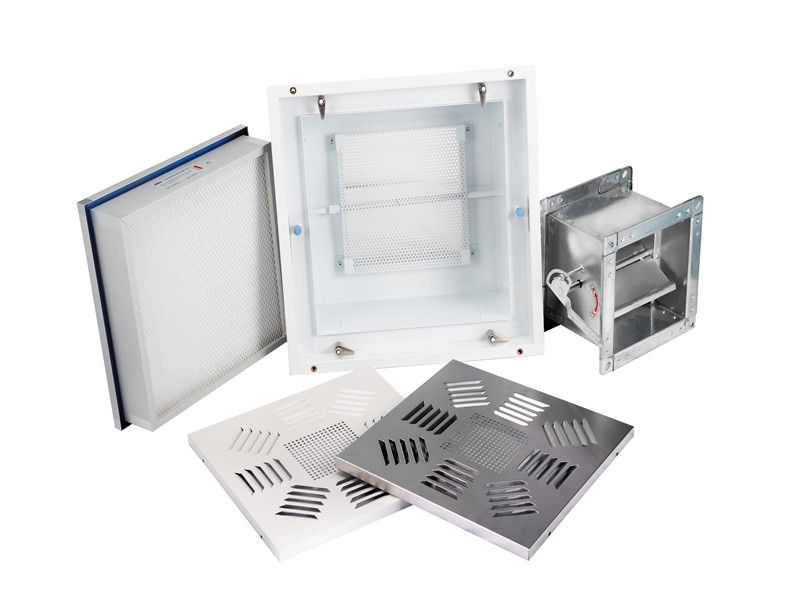
Analyze the role of chemical conversion treatment of industrial aluminum profiles.
The chemical conversion treatment of industrial aluminum profiles refers to the reaction between the surface of the aluminum profile and the oxidant in the solution in the chemical treatment solution. This chemical treatment process is not a chemical conversion film generated by applying voltage, but a conversion film generated by chemical conversion treatment. Usually referred to as conversion coating.
According to the composition of the chemical treatment solution, the chemical conversion treatment of industrial aluminum profiles can be divided into chemical oxidation treatment, chromate treatment, phosphochromate treatment and chromium-free chemical conversion treatment. The main treatment methods are:
1. Directly immerse in the chemical treatment solution.
2. Spray the chemical treatment solution on the surface of the industrial aluminum profiles.
3. Coat the high-concentration solution directly on the surface of the industrial aluminum profiles, and choose the appropriate chemical conversion treatment method according to the actual conditions. The first and second methods are more practical and the utilization rate is relatively high.
Industrial aluminum profiles must be pretreated before electrostatic spraying, and chemical conversion treatment is the main method of pretreatment. The conversion film formed by chemical conversion treatment is the result of the interaction between metal surface atoms and anions in the medium, which can be metal It is generated by pure chemical reaction with the medium, or it can be generated by electrochemical reaction. It is mainly used as a substrate coating that can be used directly, or as a bottom layer of an organic polymer coating to improve the surface of the substrate and the coating. The adhesion between the surface and the corrosion resistance, wear resistance and coloring effect of the industrial aluminum profiles.
Although the thickness of the chemical conversion film is not as good as that of the anodic oxide film, and the corrosion resistance is not as good as that of the anodic oxide film, it is simple to operate, low in cost, and does not need to add power equipment. For companies that do not require high corrosion resistance or do not need long-term use, The cost performance is still very high, very suitable for the production of high-volume, low-cost parts, and is widely used in the transportation and aerospace industries.
According to the composition of the chemical treatment solution, the chemical conversion treatment of industrial aluminum profiles can be divided into chemical oxidation treatment, chromate treatment, phosphochromate treatment and chromium-free chemical conversion treatment. The main treatment methods are:
1. Directly immerse in the chemical treatment solution.
2. Spray the chemical treatment solution on the surface of the industrial aluminum profiles.
3. Coat the high-concentration solution directly on the surface of the industrial aluminum profiles, and choose the appropriate chemical conversion treatment method according to the actual conditions. The first and second methods are more practical and the utilization rate is relatively high.
Industrial aluminum profiles must be pretreated before electrostatic spraying, and chemical conversion treatment is the main method of pretreatment. The conversion film formed by chemical conversion treatment is the result of the interaction between metal surface atoms and anions in the medium, which can be metal It is generated by pure chemical reaction with the medium, or it can be generated by electrochemical reaction. It is mainly used as a substrate coating that can be used directly, or as a bottom layer of an organic polymer coating to improve the surface of the substrate and the coating. The adhesion between the surface and the corrosion resistance, wear resistance and coloring effect of the industrial aluminum profiles.
Although the thickness of the chemical conversion film is not as good as that of the anodic oxide film, and the corrosion resistance is not as good as that of the anodic oxide film, it is simple to operate, low in cost, and does not need to add power equipment. For companies that do not require high corrosion resistance or do not need long-term use, The cost performance is still very high, very suitable for the production of high-volume, low-cost parts, and is widely used in the transportation and aerospace industries.