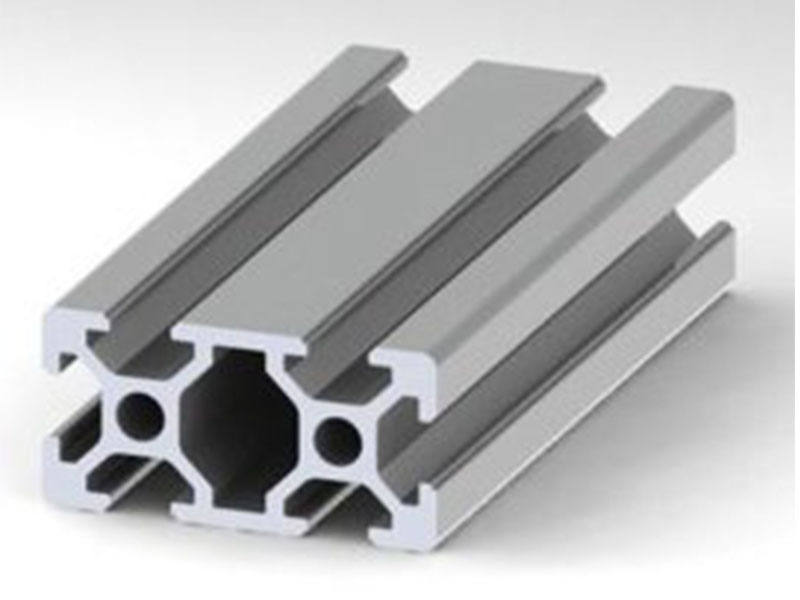
Selection factors of industrial aluminum profiles.
The scope of industrial aluminum profile is very wide, and it can be seen almost everywhere, especially in the construction industry. Now with the development of science and technology, the types of aluminum profiles are gradually increasing, and each has its own characteristics. So, how should we choose? The following briefly analyzes the method of selecting industrial aluminum profiles.
1. Strength: Strength is an important factor that must be considered during product design, especially when aluminum alloy components are used as components, the appropriate alloy should be selected according to the pressure it bears. Pure aluminum has the lowest strength, while the 2 series and 7 series heat-treated alloys have the highest degree. There is a certain relationship between hardness and strength.
2. Hardness: Many consumers are very concerned when buying industrial aluminum profiles. The hardness of the first choice is directly related to the chemical composition of the alloy. Secondly, the impact of different states is also relatively large.
3. Corrosion resistance: Corrosion resistance includes chemical corrosion and stress corrosion resistance. Generally speaking, pure aluminum of series 1 has the best corrosion resistance, series 5 performs well, followed by series 3 and 6, and series 2 and 7 are relatively poor. The selection principle of corrosion resistance depends on its use occasion. For high-strength alloys to be used in corrosive environments, various anti-corrosion composite materials must be used.
4. Weldability: There is no problem with most aluminum alloy welding lines, especially some 5 series aluminum alloys, which are specially designed for welding considerations. Relatively speaking, some 2 series and 7 series aluminum alloys are compared Difficult to solder.
5. Decorative performance: When aluminum is used for decoration or certain specific products, the surface needs to be anodized, painted, etc. to obtain the corresponding color and surface structure. At this time, its decoration should be the focus In consideration, generally speaking, materials with better corrosion resistance have excellent anodizing performance, surface treatment performance, and coating performance.
6. Machinability: Machinability includes insert forming performance and cutting performance. Because the shape is related to the state, after selecting the aluminum alloy grade, the strength range of various states needs to be considered. Generally, high-strength materials are not easy to form. It is necessary to bend, stretch, and deep-draw the aluminum material in a row. The shape of the material in the annealed state is the best. On the contrary, the shape of the heat-treated material is the worst. The machinability of aluminum alloy is relatively poor. For molds, mechanical parts, etc., the machinability is better. On the contrary, low-strength ones have poor machinability. For products that require cutting, such as molds and mechanical parts, the machinability of aluminum alloy is the most important Considerations.
1. Strength: Strength is an important factor that must be considered during product design, especially when aluminum alloy components are used as components, the appropriate alloy should be selected according to the pressure it bears. Pure aluminum has the lowest strength, while the 2 series and 7 series heat-treated alloys have the highest degree. There is a certain relationship between hardness and strength.
2. Hardness: Many consumers are very concerned when buying industrial aluminum profiles. The hardness of the first choice is directly related to the chemical composition of the alloy. Secondly, the impact of different states is also relatively large.
3. Corrosion resistance: Corrosion resistance includes chemical corrosion and stress corrosion resistance. Generally speaking, pure aluminum of series 1 has the best corrosion resistance, series 5 performs well, followed by series 3 and 6, and series 2 and 7 are relatively poor. The selection principle of corrosion resistance depends on its use occasion. For high-strength alloys to be used in corrosive environments, various anti-corrosion composite materials must be used.
4. Weldability: There is no problem with most aluminum alloy welding lines, especially some 5 series aluminum alloys, which are specially designed for welding considerations. Relatively speaking, some 2 series and 7 series aluminum alloys are compared Difficult to solder.
5. Decorative performance: When aluminum is used for decoration or certain specific products, the surface needs to be anodized, painted, etc. to obtain the corresponding color and surface structure. At this time, its decoration should be the focus In consideration, generally speaking, materials with better corrosion resistance have excellent anodizing performance, surface treatment performance, and coating performance.
6. Machinability: Machinability includes insert forming performance and cutting performance. Because the shape is related to the state, after selecting the aluminum alloy grade, the strength range of various states needs to be considered. Generally, high-strength materials are not easy to form. It is necessary to bend, stretch, and deep-draw the aluminum material in a row. The shape of the material in the annealed state is the best. On the contrary, the shape of the heat-treated material is the worst. The machinability of aluminum alloy is relatively poor. For molds, mechanical parts, etc., the machinability is better. On the contrary, low-strength ones have poor machinability. For products that require cutting, such as molds and mechanical parts, the machinability of aluminum alloy is the most important Considerations.